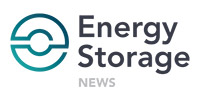
In 30 years since commercialisation, lithium-ion (li-ion) batteries have been used in an increasingly diverse range of products, starting from early generation handheld electronics to powering cars and buses. Additionally, these batteries are increasingly sought after for utilisation in energy storage applications, often paired with renewable energy generation. The continued decline in battery prices combined with the global trend toward energy grids being powered by renewable energy sources is predicted to increase the world’s cumulative energy storage capacity to 2,857GWh by 2040 [1], a substantial increase from the current capacity of ~545MWh [2], according to recent estimates by Bloomberg New Energy Finance.
These staggering projections paint an encouraging picture for how prominent li-ion-driven energy storage applications will become in the future as the world increases usage of renewable, clean energy sources to power energy grids worldwide. Driven increasingly by electro-mobility as well as grid-scale energy storage applications, the volume of li-ion battery cells being sold is set to surge. The graph in Figure 2 contextualises the relative volume (in tonnes) of new li-ion battery cells forecasted to be sold through to 2025. The growing quantities of li-ion batteries being placed on the markets accelerates the urgency with which the world must find an economically viable, commercial-scale recycling solution for end-of-lifecycle li-ion batteries to be recycled at a ‘mega’ scale. This article will take a closer look at some of the challenges that exist today within the li-ion recycling sector and where opportunities exist to overcome the current roadblocks.
Li-ion recycling industry challenges
Feed Sourcing
Secondary resource recovery (i.e. recycling) has a set of unique operational challenges that need to be addressed concurrent to the development of an economic, advanced technology. For the purpose of recycling, feed materials are typically inherently distributed, making it difficult to collect a high volume of feed for a processing plant. Although the collection supply chains for some analogous industries such as lead-acid battery recycling are well-established and mature by comparison, the li-ion battery recycling supply chain continues to be fluid. Spent li-ion battery sources can be broadly segmented into portable/’small format’ and ‘large format’ sources, which corresponds to the relative voltage of li-ion batteries (i.e. low voltage and intermediate to high voltage, respectively). Each of these types of batteries has a diverse group of stakeholders – from manufacturers, to the dealer network, recycling programmes, electronics and vehicle recyclers. In the context of the energy storage sector, its own diverse group of stakeholders exists – battery technology provider, energy storage integrator, project developer and asset owner. Managing the inherently heterogenous nature of li-ion batteries from a wide range of stakeholders remains a central challenge for companies in the li-ion resource recovery industry.
Logistics and regulations
Li-ion batteries are currently classified as Class 9 Dangerous Goods due their dual chemical and electrical hazard. Li-ion batteries can possibly undergo thermal runaway, typically resulting from internal shorting, leading to fire or explosion. There are numerous factors that can cause thermal runaway, including but not limited to overcharging, environmental conditions (e.g. extreme external temperatures) and manufacturing defects. At the onset of thermal runaway, the battery heats in seconds from room temperature to above 700°C. As part of this complex set of chemical reactions, the electrolyte solvent in lithium-ion batteries – typically alkyl carbonate-based – acts as a ‘fuel’ source for combustion.