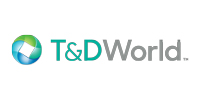
More than 700 MW of utility-scale battery capacity has been installed in the United States, 80% of which is based on Lithium-ion chemistry. For lithium-ion batteries to secure their place as a global energy infrastructure staple, there is a real and growing need for a robust supply chain that includes end-of-life processing that is both efficient and cost-effective.
The rise of Li-ion battery formats rich in cobalt for applications in the vehicle and stationary power storage markets has caused periodic commodity price spikes that are a major cause of anxiety for OEMs who are unable to pass along the added costs. Battery recycling presents an opportunity to hedge against commodity fluctuations by tapping into existing material stockpiles in the form of end-of-life batteries and manufacturing scrap.
China has emerged as a leading nation in the rollout of renewable technology, becoming the largest market for renewable generation, electric vehicles, and Li-ion batteries. Hungry for resources to fuel its economic and infrastructure expansion, China has been investing to secure mineral resources across the world and has made Li-ion battery recycling mandatory. With more than $10,000 of material value in every ton of Li-ion batteries, it is no wonder that many companies have been investing heavily in recycling technologies and it seems only a matter of time before Li-ion batteries recycling is mandatory in the United States.
However, batteries have compact and complex architectures, layering high-grade materials in thin layers encased in much lower value commodity components such as aluminum, copper, and plastic films making them difficult to process efficiently. Also, rapid innovation in the battery industry means that for a recycling process to be scalable, it must be able to handle a broad range of physical formats and evolutions in composition.
One of the most widely deployed methods of Li-ion battery recycling is pyrometallurgical, where Li-ion batteries are incinerated in a blast furnace to recover the nickel and cobalt as an alloy. Recently some practitioners have reported being able to recover lithium from the resultant slag. The companies deploying this technique typically have a large book of assets and experience in operating these systems and are able to efficiently transition these high cap-ex assets to capture some of the metal value from these Li-ion battery material streams. While this technique can accept most any Li-ion battery format and has little preprocessing required, it releases one ton of CO2 for every ton of batteries processed and fails to capture a significant fraction of the economic value.