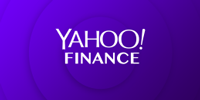
Sydney, Australia, May 15, 2020 – (ABN Newswire) – Ground breaking research recently completed by a leading German battery technology institute has identified a previously unrecognised contamination and safety risk for lithium-ion batteries – the use of lower purity (grade) alumina in battery cell manufacture.
The Fraunhofer Institute for Ceramic Technologies and Systems IKTS in Dresden Germany, recently completed test work that has the potential to rock the lithium-ion battery industry.
Globally, lithium-ion battery production is rapidly expanding to meet the burgeoning demand from electric vehicles (EV’s) and portable electronic devices. The Fraunhofer ITKS research was triggered because a significant part of the industry, including those that supply EV batteries, are turning to cheaper substitutes such as low grade alumina and boehmite as the coating material on battery separator sheets and composite separators. However, this hot-off-the-press German research brings into question the safety of using lower quality separator coating materials.
A lithium-ion battery stores then releases power by lithium ions moving between the battery cathode and anode, representing the charge and visa-versa discharge cycles. Separating the cathode and anode within the battery is a liquid electrolyte and a thin polymer sheet through which lithium ions pass – a separator sheet. The composition of these polymer separator sheets has evolved over time in parallel with increases in battery energy density and faster charging requirements. Now separator sheets are mostly coated with thin layers of alumina powder to maintain separator integrity under the ever-increasing operating temperatures of modern high-energy lithium-ion batteries.
Wisely it would seem, the lithium-ion battery industry initially adopted high grade 4N alumina (99.99%) as the standard coating material for separator sheets, especially where battery safety was paramount – such as in EV’s. The scientific tests recently completed by the Fraunhofer IKTS plainly vindicate the initial choice of 4N alumina by the battery industry. In its tests, the Institute exposed various commercially available lower grades of alumina / boehmite powders to lithium battery electrolyte solution under controlled battery type conditions. What was observed was extremely concerning – the severe leaching of sodium from the lower grade alumina’s into the organic electrolyte solution, which resulted in significant electrolyte contamination.
Specifically, the research reported that in its test of 3N alumina (99.9% alumina) the sodium content within the electrolyte solution rose from an acceptable 0.5 ppm up to a potentially catastrophic level of 40 ppm (an 80-fold increase). Similar leaching was observed for boehmite (99.7% alumina), where the level of sodium in the electrolyte jumped 20-fold. As a base line, sodium leaching from 4N alumina (99.99%) into the electrolyte is negligible, as there is virtually no sodium present in the 4N product.
Sodium contamination is one of the major no no’s for anywhere within a lithium-ion battery. Sodium can dramatically reduce battery discharge capacity and adversely affect the reactivity of lithium ions. When too much sodium is present in a battery’s organic electrolyte solution, the movement of lithium ions is hindered and the discharge capacity is rapidly reduced; the performance of the battery is compromised. Lithium-ion battery end-users such as EV assemblers or high-end portable electric device manufactures would never accept a battery with an electrolyte solution containing 40ppm sodium – yet it would seem that this is where they are set to end up if 3N alumina / boehmite is adopted by industry as a coating on battery separator sheets.